FDM ist ein vergleichsweise sehr einfaches Druckverfahren mit geringen Anschaffungskosten und gut geeignet für den Prototypenbau. Das Grundprinzip des Drucks Layer um Layer „nach oben“ bedingt Berücksichtigungen in der Konstruktion der Druckkörper. So ist die Belastbarkeit in der Layerebene in der Regel vielfach höher als zwischen den Layern und Layer können nicht einfach „freischwebend in der Luft“ gedruckt werden. Auf der anderen Seite kommen beim FDM-Verfahren thermoplastische Kunststoffe zum Einsatz, unter ihnen finden sich äußerst stoßfeste Kunststoffe wie Polyamide (Nylon) und gerade der Druck von großen Ebenen ist vergleichsweise einfach im Vergleich zu anderen Verfahren.
Zum Einstieg ein einfaches Beispiel, hier das Unterteil eines Messarms. An dieser Stelle soll nicht durch funktionale Einzelheiten vom Thema abgelenkt werden. Das Teil muss bei seinem Einsatz starke Scherkräfte an der Oberseite verkraften. Es besteht aus einem zylindrischen Teil auf einer Bodenplatte und vier seitlichen Stützstrukturen. Diese verringern die Scherkräfte zwischen dem zylindrischen Teil und der Bodenplatte, welche sonst ungünstig zwischen den Layern wirken würden.
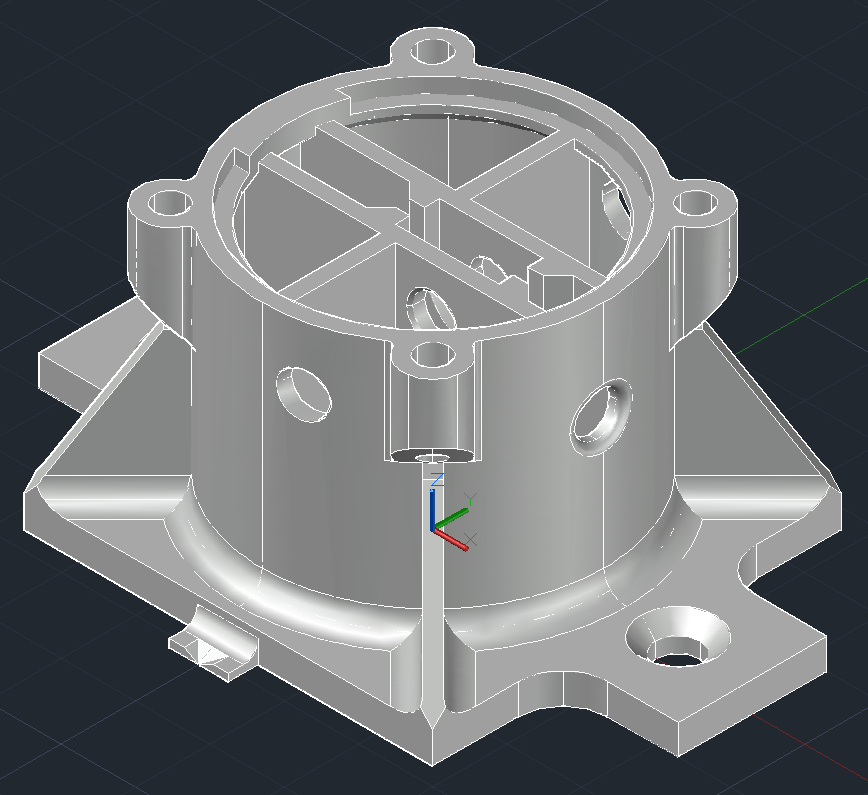
Weiter ist der Übergang zwischen Bodenplatte und dem zylindrischen Teil abgerundet, wie bei einer Schweißnaht. An dieser Stelle sind die Scherkräfte am höchsten und es besteht die Gefahr, dass sich die Layer an dieser Stelle lösen.
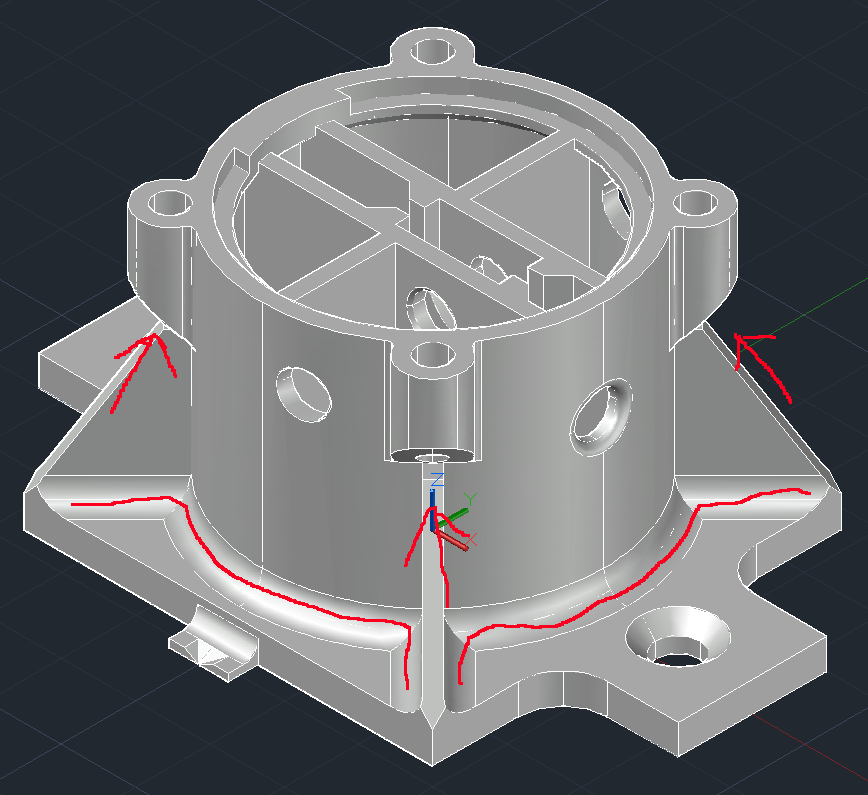
Weiter befinden sich am oberen Ende des zylindrischen Teils vier Aufnahmen für Einpressmuttern, im Bild mit Pfeilen gekennzeichnet. Die Art ihrer Konstruktion ermöglicht einen Druck ohne Stützstrukturen. Sie entwachsen dem zylindrischen Teil mit 45° an der Unterseite. Dieser Winkel ist ohne Stützstruktur in FDM problemlos druckbar.
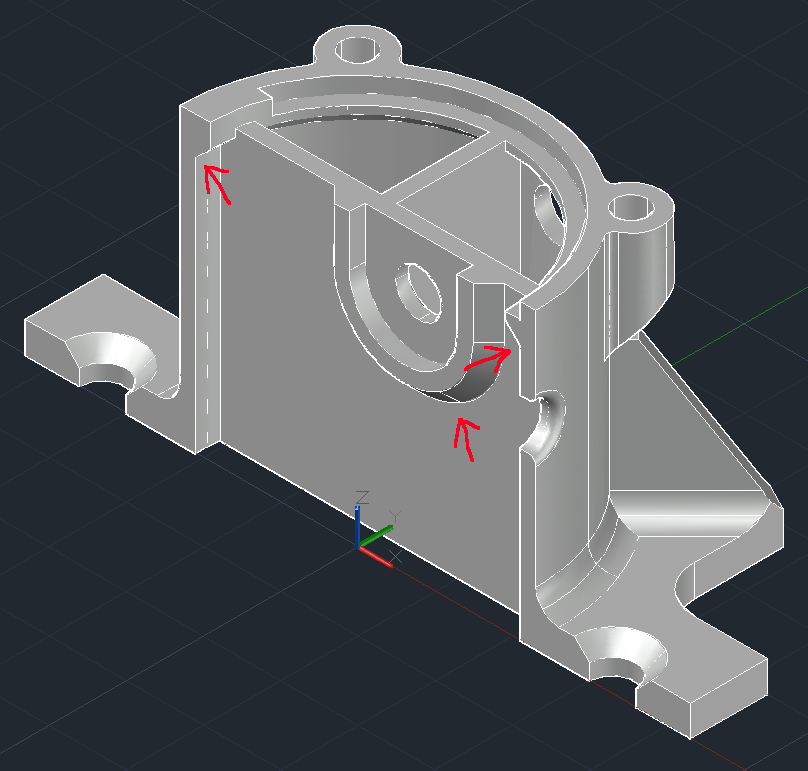
Dieses Bild zeigt wieder den Einsatz von Schrägen, um ohne Stützstrukturen Verdickungen zu realisieren.
WICHTIG: Löcher für die Aufnahme von Schrauben etc. sollten immer zumindest annähernd der Z-Achse ausgerichtet werden. Löcher zwischen Layern sind immer problematisch, Hebelkräfte können hier schnell die Layer reißen lassen.
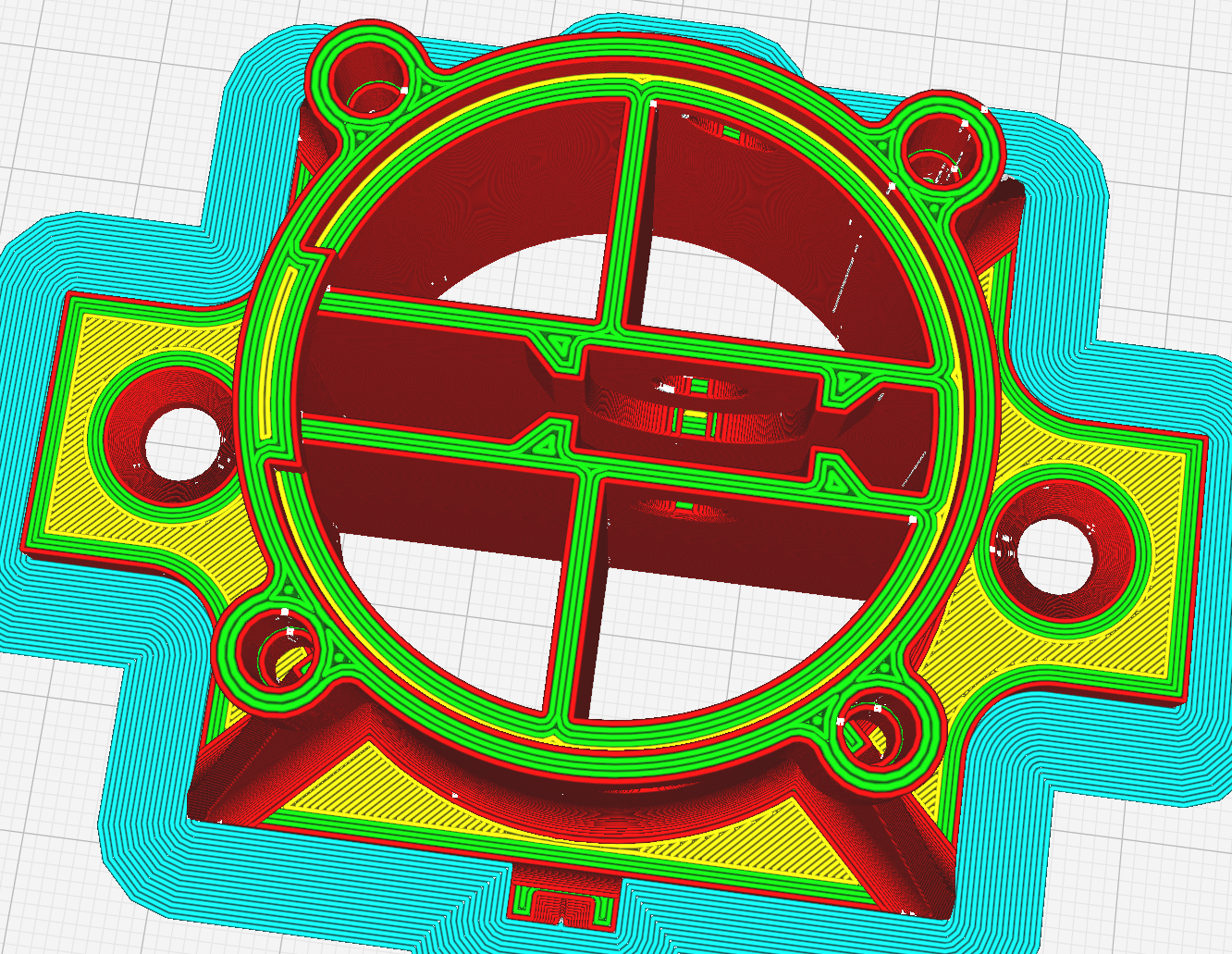
Dieses Bild zeigt den geplanten Druckvorgang durch den Slicer. Zu sehen sind die geschlossenen Spuren um die Löcher für die Einpressmuttern. Diese geschlossenen Spuren können große Zugkräfte aufnehmen, im Gegensatz zu Zugkräften zwischen den Layern. Druckkörper sollten daher immer so konstruiert werden, dass Zugkräfte auf geschlossene Spuren treffen.
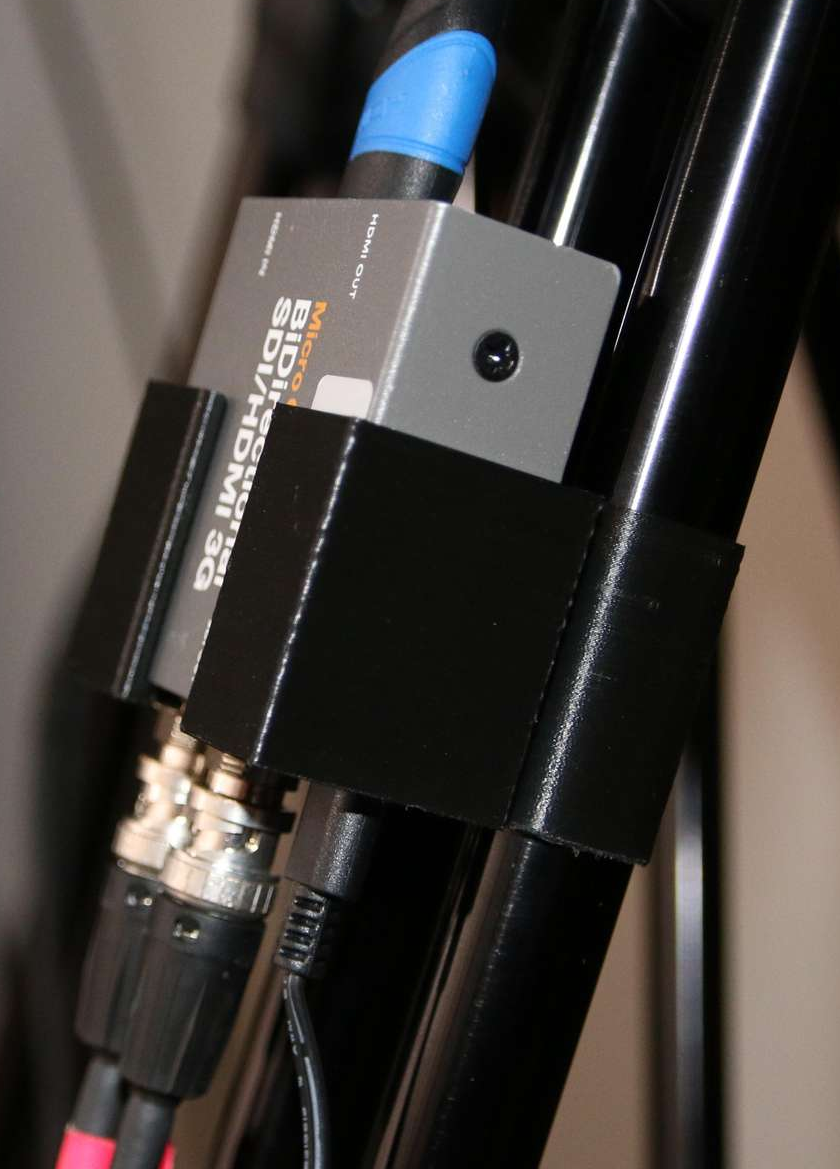
Dieses Bild zeigt einen Halter mit Klammern aus Nylon.
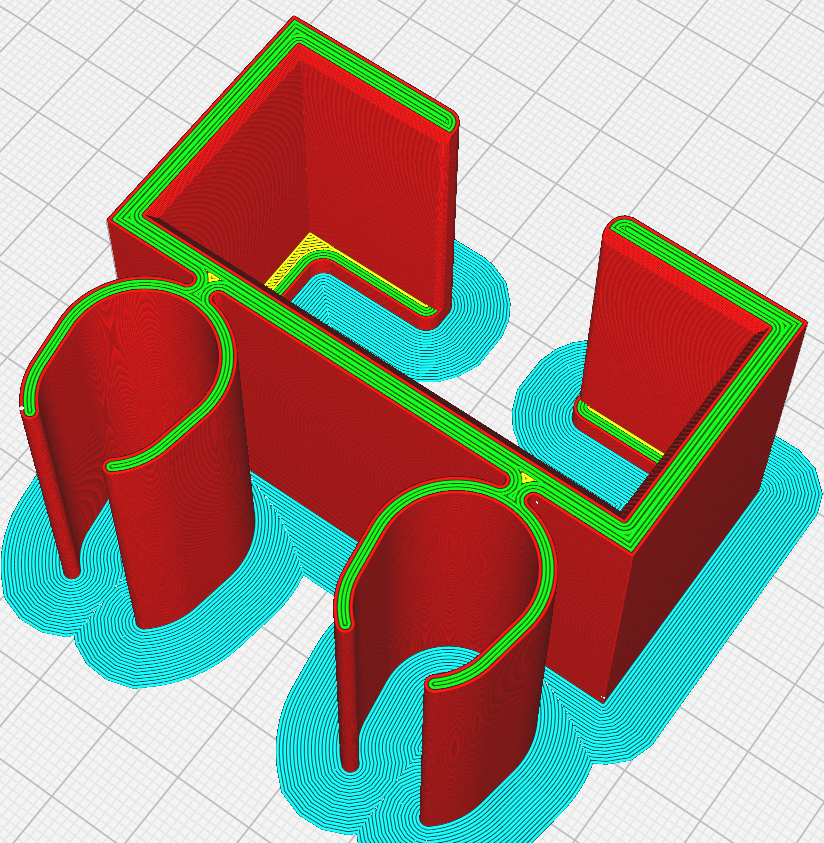
Wieder ist zu sehen, wie die Zugkräfte, in diesem Fall auf die Klammern wirkend, in den Layerebenen und nicht zwischen diesen liegen.
In vielen Fällen ist es dazu besser, ein Bauteil in Einzelteile zu zerlegen, welche einzeln mit jeweils optimaler Ausrichtung gedruckt und dann zusammen montiert oder verklebt werden. Dazu ein einfaches Beispiel einer Kabelschürze für ein Videostativ:
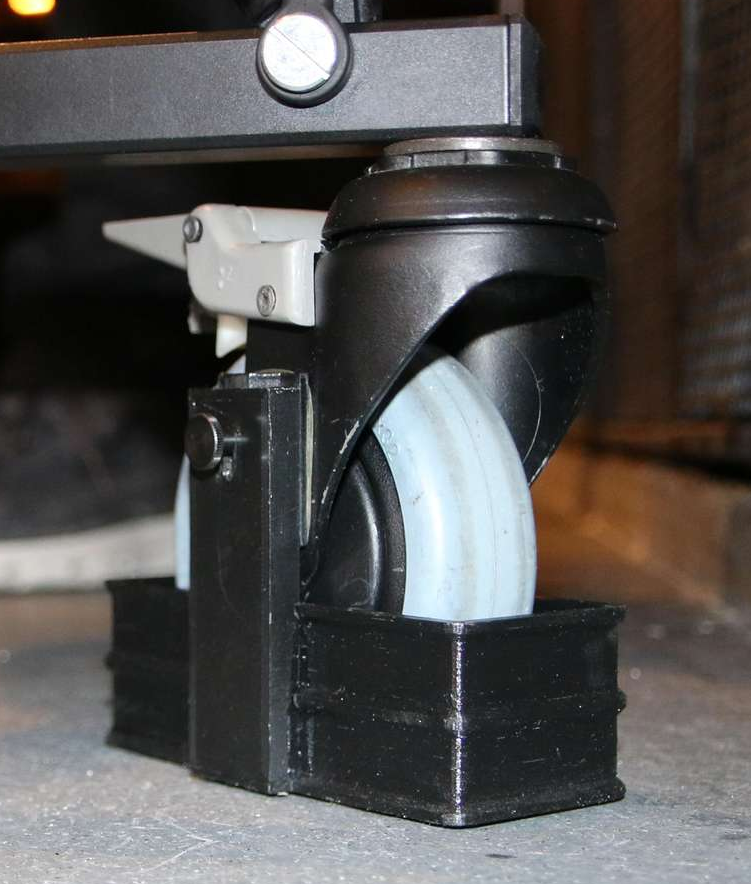
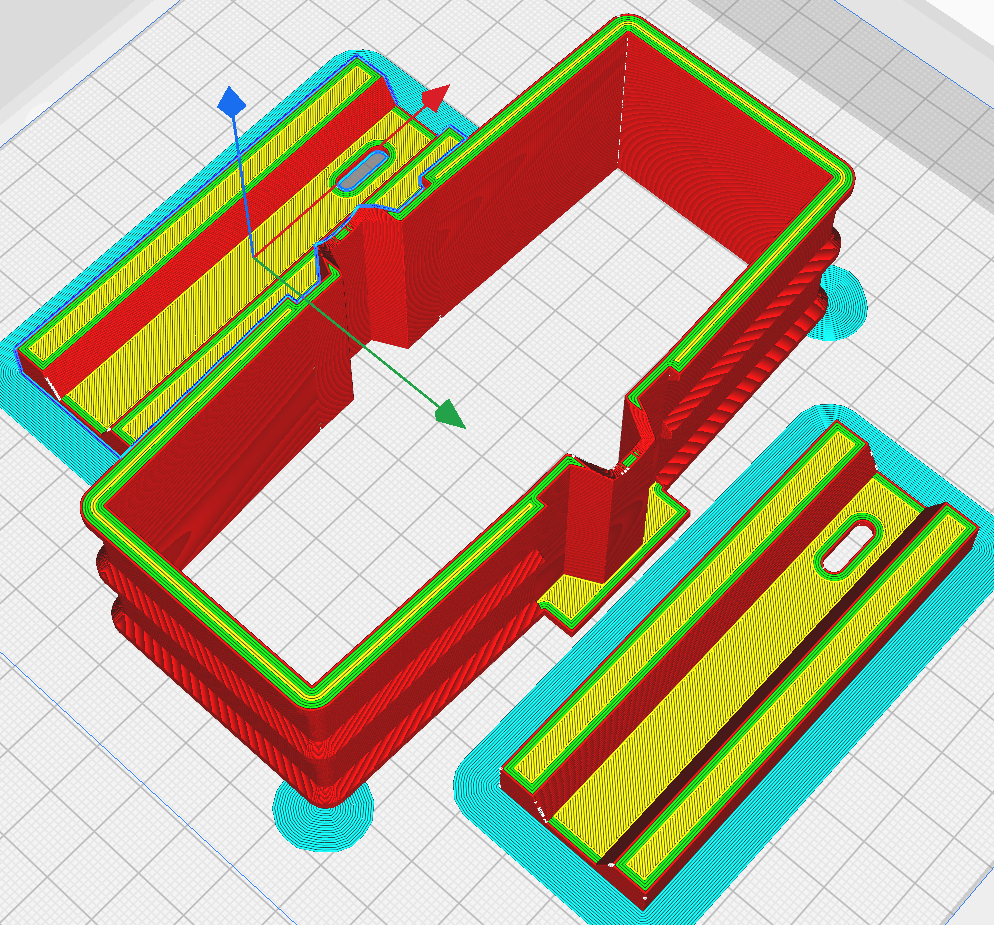
Die Schürze und ihre Stege sind als drei Körper zerlegt. Durch diese Zerlegung werden die Kräfte wieder ideal in den Layerebenen abgetragen. Auch die Langlöcher verlaufen so wieder ideal in der Z-Achse. Nach dem Druck werden die Teile verklebt und ergeben das so optimierte Bauteil.
Nicht immer lassen sich aber alle Löcher eines Körpers ideal ausrichten. Dazu wieder ein praktisches Beispiel:
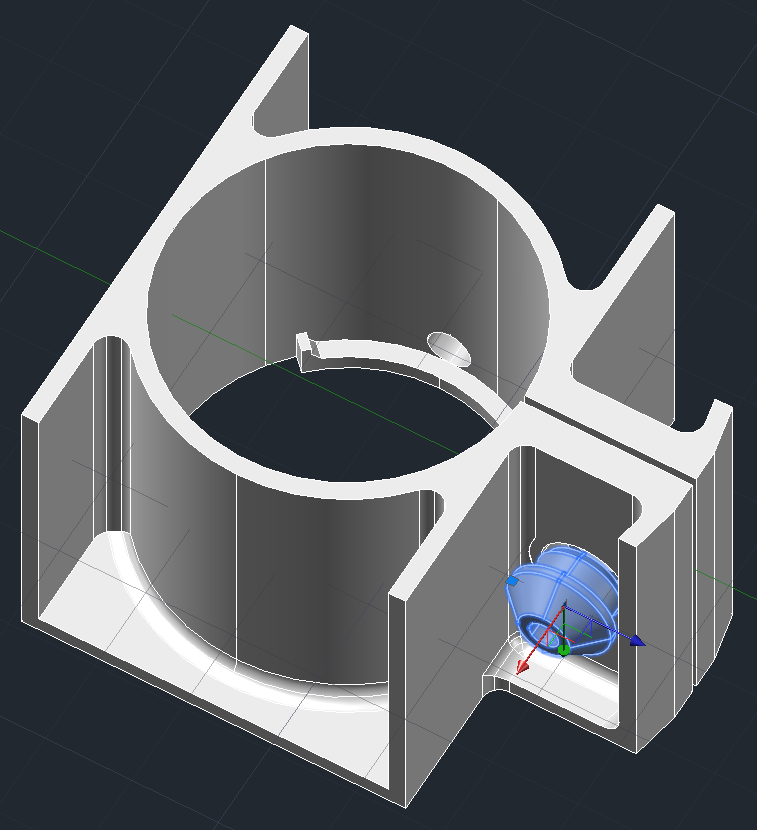
Das Bild zeigt eine Rohrspange. Die Kräfte werden wieder in den Layerebenen abgetragen. Problematisch ist aber die Verschraubung rechts im Bild. Hier verläuft das nötige Loch zwischen den Layern. So würde es hier zum Riss der Layer kommen. Dies wird durch zwei zusätzliche Teile verhindert, im Bild blau zu sehen. Sie werden wieder ideal ausgerichtet, einzeln gedruckt und dann mit der Spange verklebt.
Die Zerlegung in Einzelteile erlaubt eine ganze Reihe von Konstruktionen, welche sonst schwer oder nicht druckbar wären. Nuten erlauben dabei die genaue Ausrichtung für die Verklebung. Dazu wieder ein Beispiel:
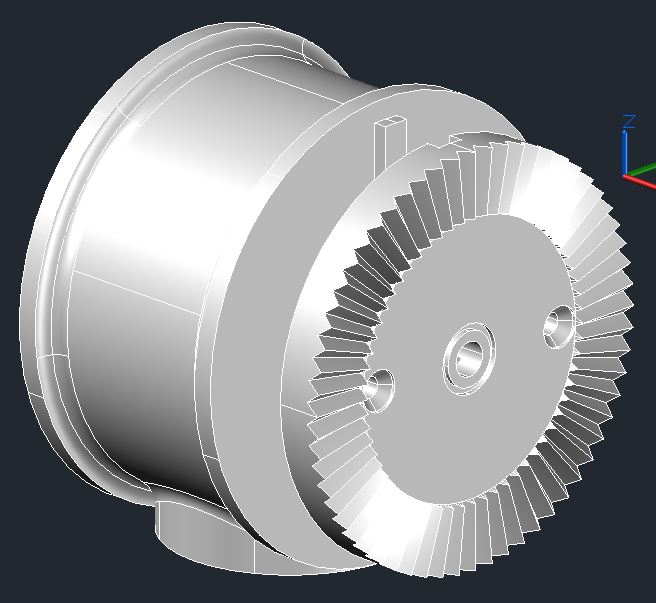
Problematisch sind immer einzeln stehende Stege. Diese brechen schnell zwischen den Layern. Stege sollten daher immer seitlich „abgefangen“ werden, z.B. mit einem Rahmen:
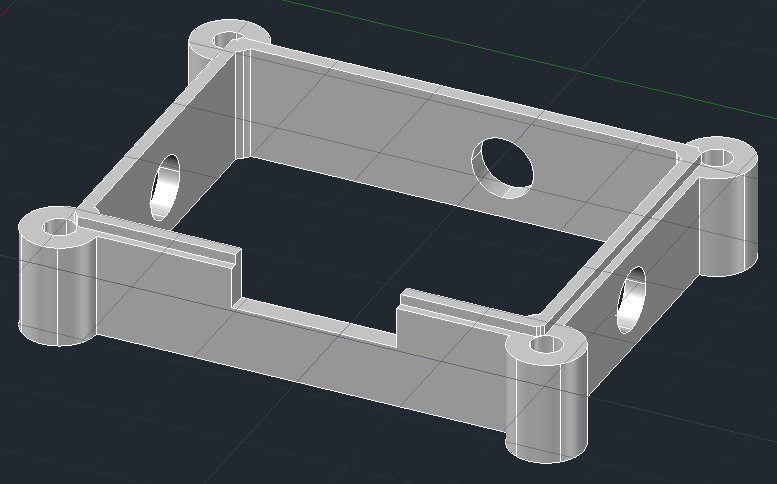
Bei Berücksichtigung dieser Punkte kann FDM gerade seine Vorteile ausspielen. Es lassen sich geometrisch komplexe Teile drucken, welche z.B. im Spritzguss nur schwer oder gar nicht realisierbar wären, oft bei richtiger Konstruktion ohne Stützstrukturen. Hier als Beispiel ein Adapter zwischen zwei Geräten mit unterschiedlichen Querschnitten:
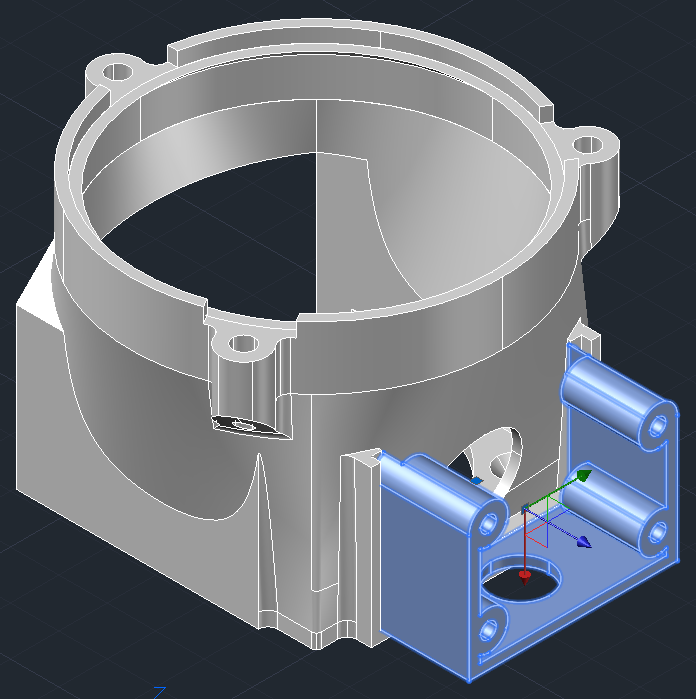
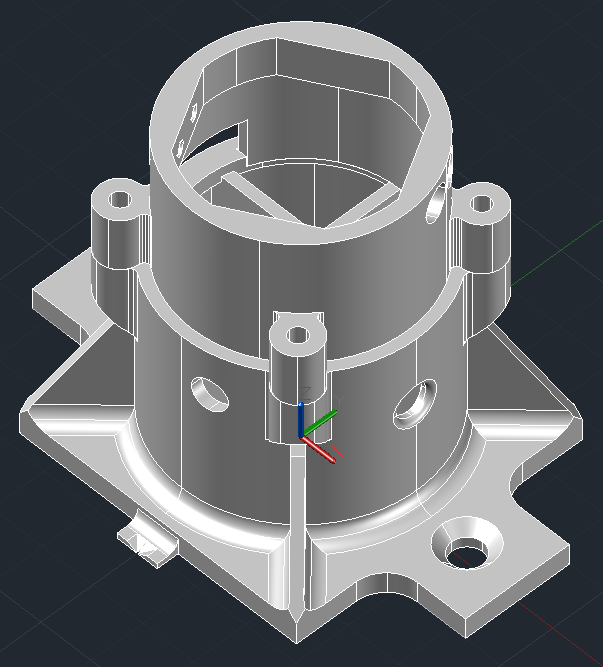
Vergleichsweise kleine oder massive Körper lassen sich auf diese Weise in einem Stück drucken. Bei größeren Körpern vor allem mit dünnen Wänden wird dies immer problematischer. Hier bietet aber FDM gerade wieder eine funktionsbedingte Stärke, das Drucken von großen ebenen Platten, welches gerade bei anderen Druckverfahren wie SLA, SLS, MJF etc. schwierig ist. Als Einstieg das Bild eines Funktionsprototyps, alle Kunststoffteile sind mit FDM in ASA gedruckt:
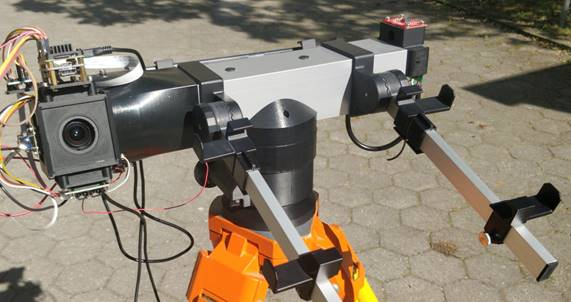
ASA (Acrylnitril-Styrol-Acrylat) wird gern als das „ABS für draußen“ bezeichnet. Es ist ein langlebiges Filament, das gegen Witterungsbedingungen wie UV-Strahlung, Temperatur und Luftfeuchtigkeit beständig ist und auch noch weniger Verzug beim Druck aufweist. Seine Layerhaftung ist allerdings nicht mit PETG/CPE/PCTG oder PA vergleichbar, dafür lassen sich höhere Genauigkeiten erreichen bis in den Zehntel-Millimeter-Bereich und die Verklebung ist einfacher.
ASA eignet sich hervorragend für Funktionsprototypen im Rahmenbauweise. Dazu zunächst eine Abbildung der Konstruktion des Messkopfes:
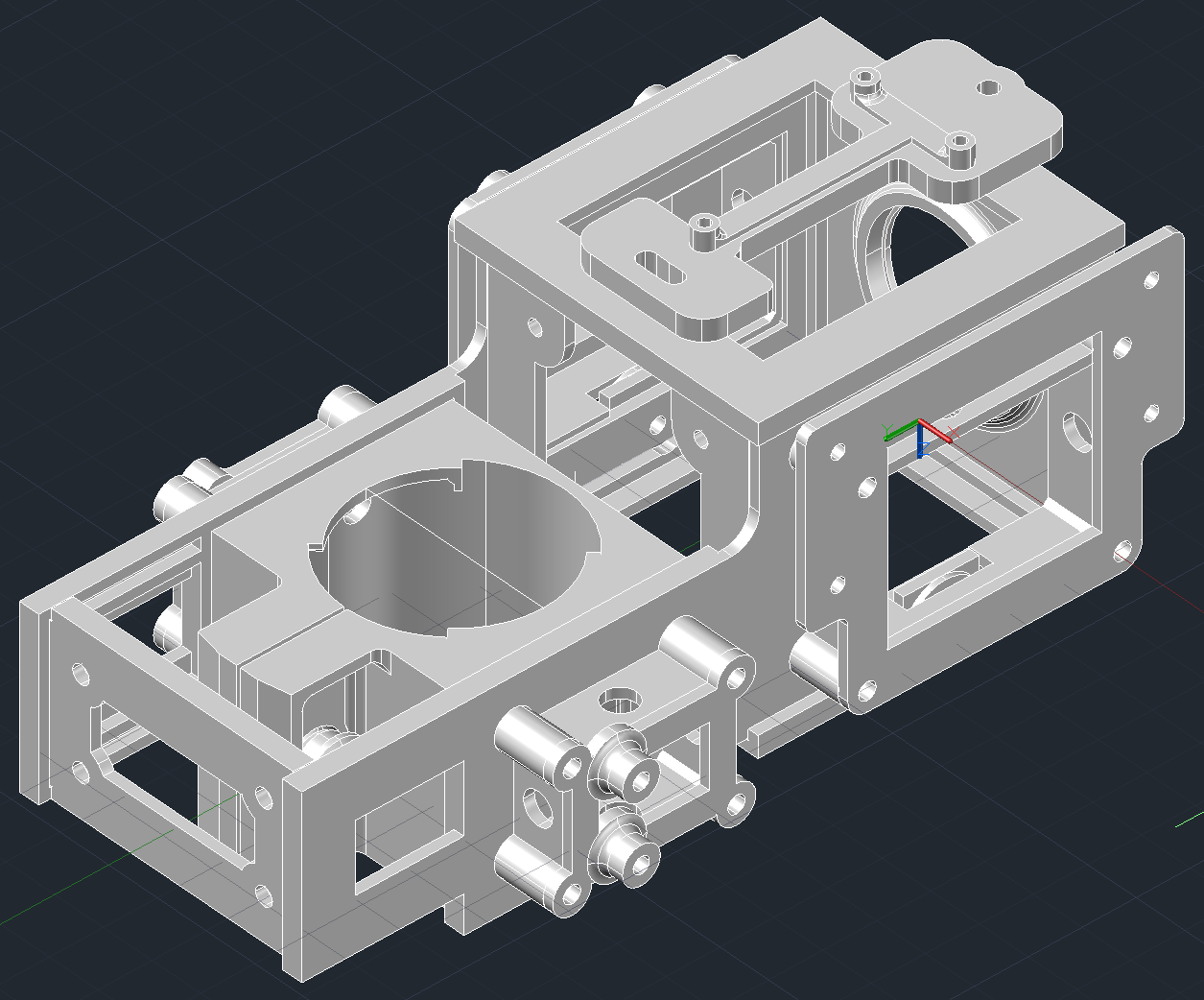
Der Messkopf besteht aus lauter einzelnen Platten, welche zusammengeklebt als Rahmen die Stabilität der Konstruktion ergeben. Jede Platte ist dabei sehr stabil, da die Kräfte immer in der XY-Ebene der Platte, also innerhalb der Layerebenen auftreten. Die folgenden Abbildungen zeigt ein paar einzelne Platten und Anbauten:
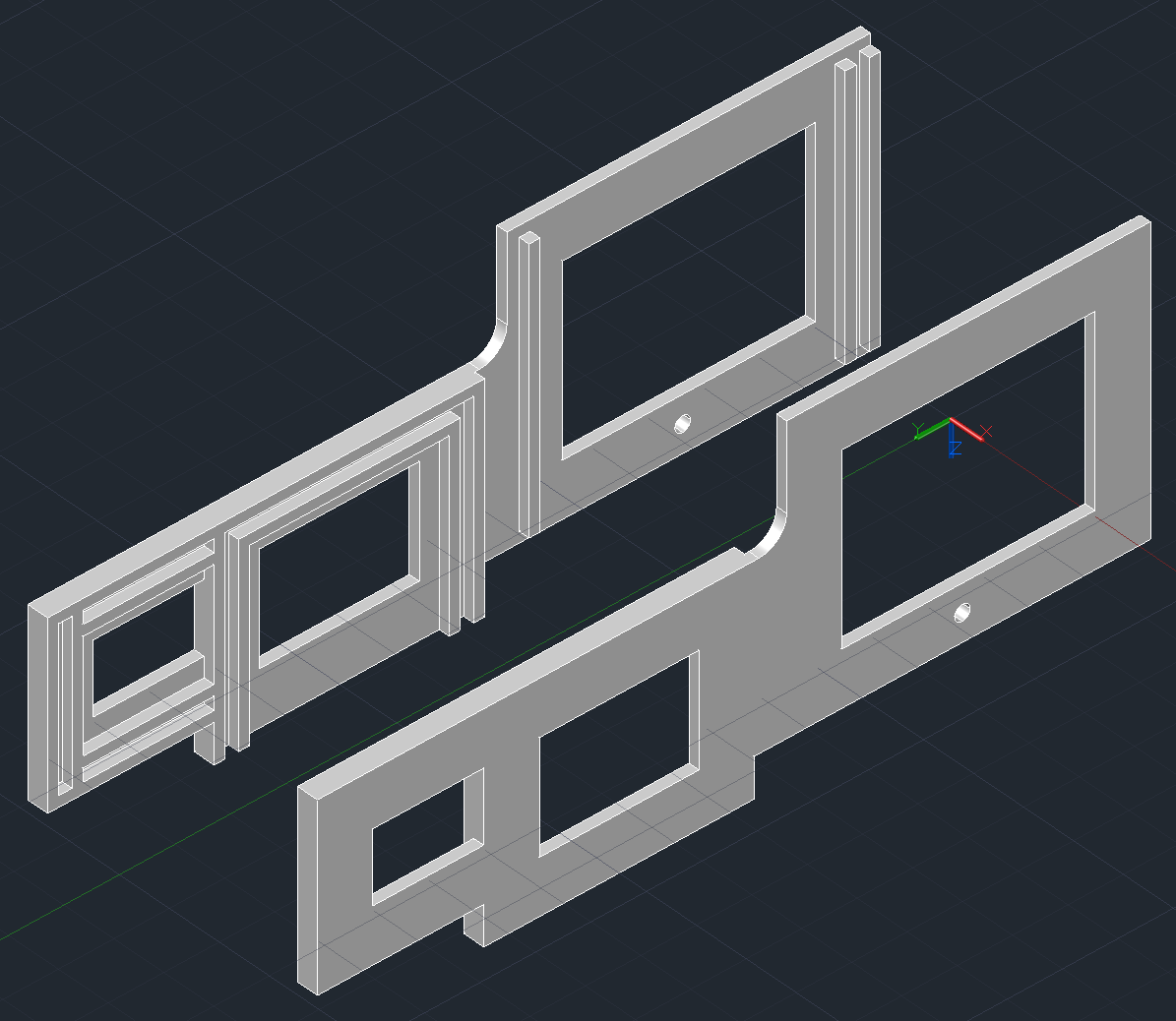
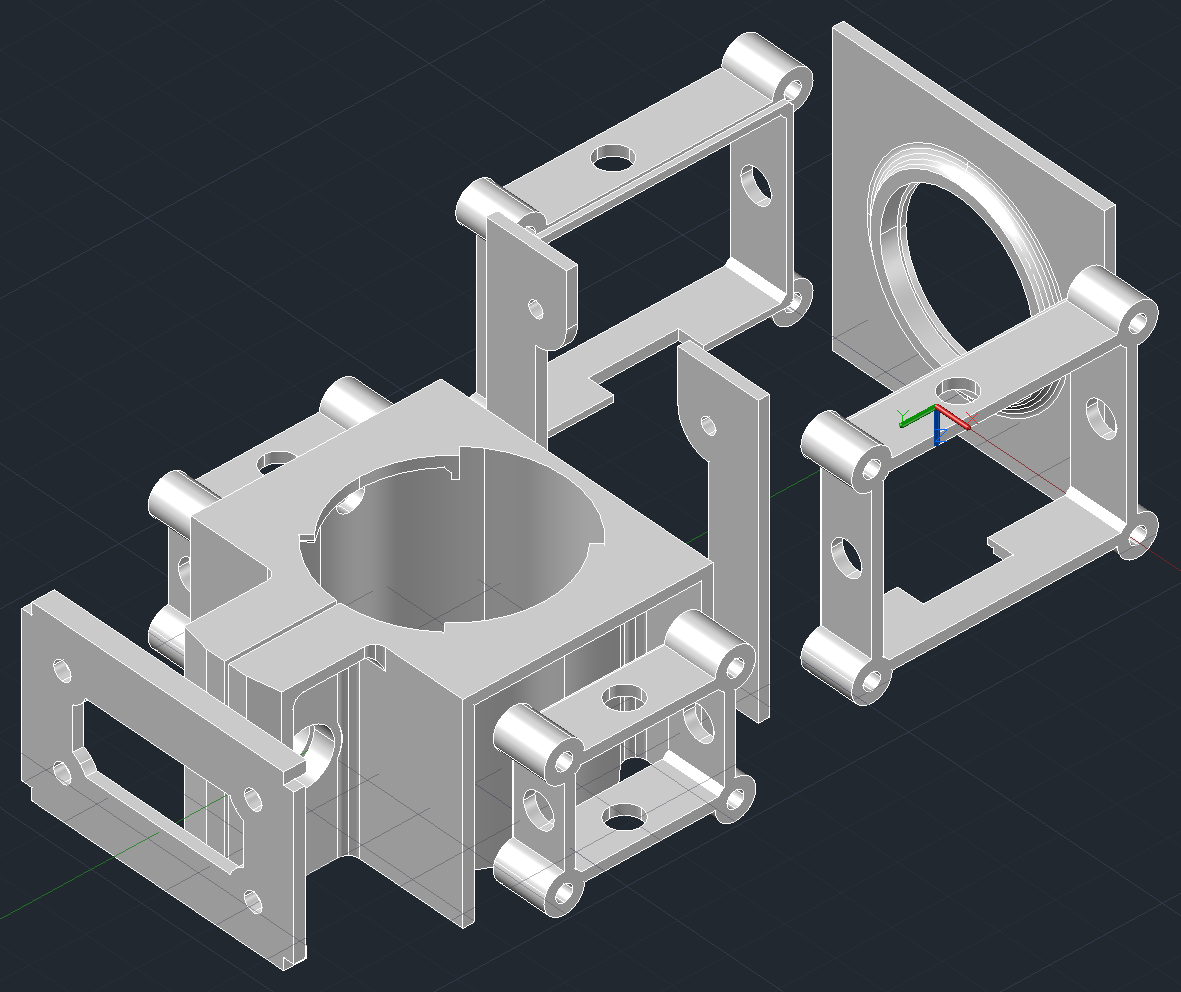
Verklebt ergeben diese Elemente bei geringem Gewicht hohe Stabilität. Durch das beidseitige Verkleben von Aufbauten besteht auch wieder in den meisten Fällen keine Notwendigkeit von Stützstrukturen beim Druck.
Solche Platten lassen sich auch sehr stabil in Wabenstrukturen oder Dreiecksstrukturen ausführen, hier in diesem Beispiel gleichzeitig als Lüftungsschlitze mit Spritzwasserschutz:
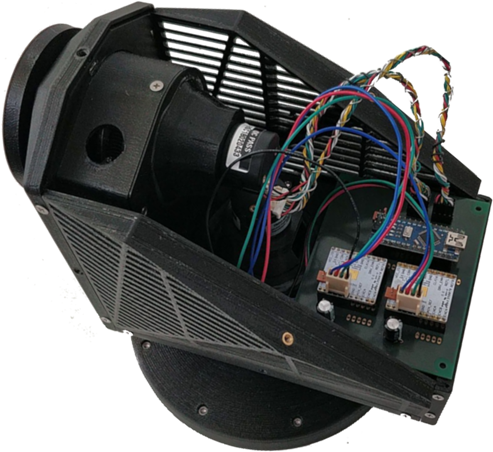
Schwieriger fallen sehr filigrane Strukturen aus.
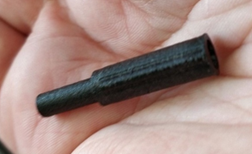
Hier als Beispiel eine biegsame Welle aus Nylon für Stepper. Diese benötigt durch die Konstruktion im Gegensatz zu Lösungen aus Metall keine Feststellschraube, ist wesentlich leichter und kleiner:
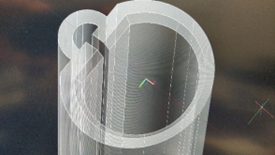
Bei solchen dünnwandigen Ausführungen kommt es auf eine genaue Abstimmung von Modell und Druckerkonfiguration an. Das Modell selbst ist in den Wandstärken an die Druckdüse und die Führung ausgelegt, kleine Änderungen entscheiden zwischen sehr gutem Ergebnis und Totalausfall. In diesem Bereich muss die Konstruktion daher direkt auf den verwendeten Drucker zugeschnitten sein. In diesem Fall lassen sich aber selbst filigran komplexe Lösungen wie etwa dieser Zahnkranz bei einem Schneckengetriebe realisieren:
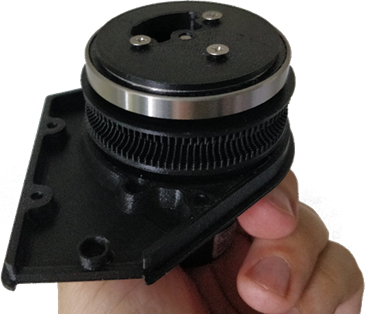
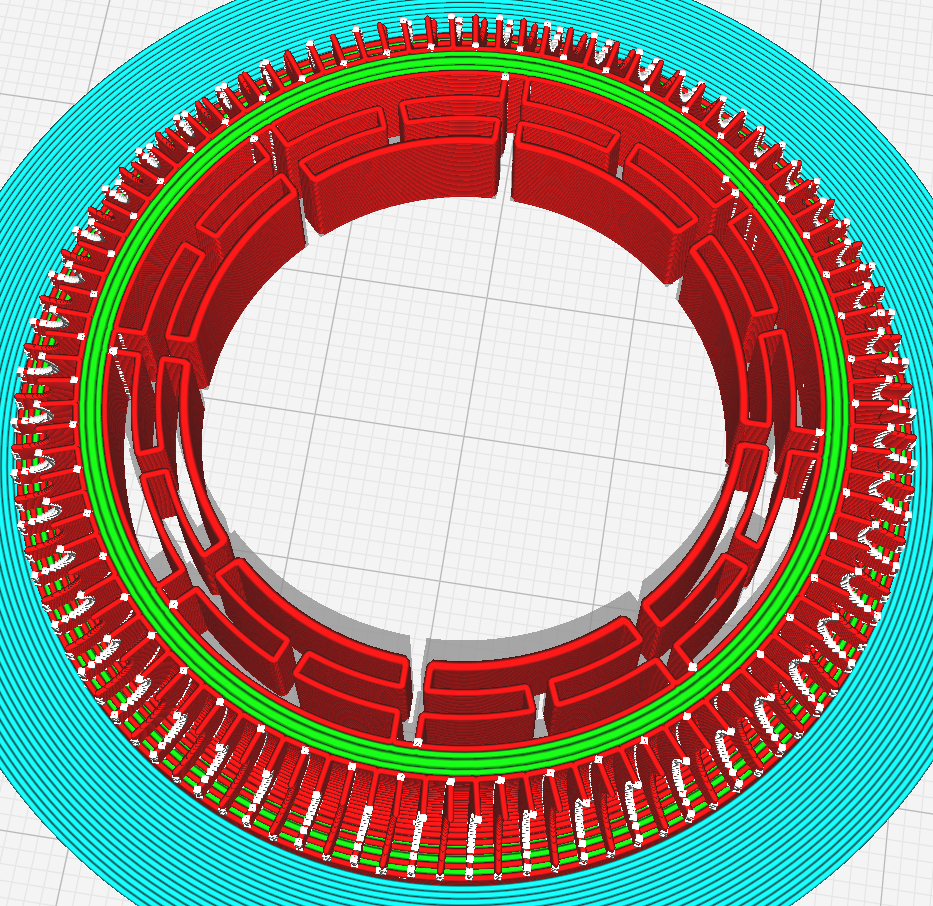
Bei vielen Materialien ist auch Smoothing möglich, die Behandlung der Oberfläche mit Dämpfen von Lösungsmitteln. Dies ist auch bei anderen Druckverfahren wie MJF oder SLS üblich:
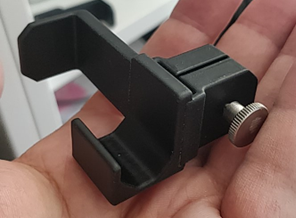
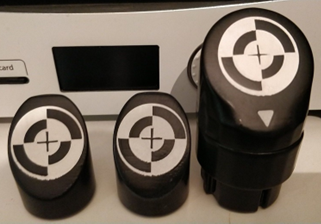
Lösungsmittel sind auch die Lösung für Problemstellungen wie den Gewindeschnitt. Gerade feine Gewinde lassen sich in FDM schlecht direkt drucken. Bei Materialien wie ABS und ASA kann der Gewindeschnitt schnell zum Reißen der Layer führen. Hier hilft die Vorbehandlung der Gewindelöcher mit einem Lösungsmittel wie Dichlormethan. Dieses verbindet die Layer im Loch zusätzlich und dringt tief in das Material ein. Nach einer längeren Abbindezeit, bei welcher der Kunststoff noch nicht wieder völlig abgebunden ist, wird der Gewindeschnitt durchgeführt. So ergeben sich saubere und stabile Gewindegänge.
Ebenfalls möglich ist der unterbrochene Druck mit Einsetzung von Trägerstrukturen etc. Dazu muss dem Drucker entsprechend der G-Code modifiziert werden. Der Drucker stoppt, die Teile werden eingesetzt, der Drucker druckt auf diesen weiter. Auch auf diese Weise können Stützstrukturen vermieden und auch saubere, glatte Unterseiten von Brücken und Überhängen realisiert werden. Gerade bei schwierig zu verklebenden Kunststoffen wie Nylon ist diese Technik ein möglicher Ausweg.
Bei Kunststoffen wie PETG bietet sich auch eine Verklebung mittels Dichlormethan an. Dieses sehr leicht flüchtige Lösungsmittel hat hohe Kriecheigenschaften. Bei der Konstruktion der zu verklebenden Teile kann dies für entsprechende Führungskanäle genutzt werden, durch welche das Dichlormethan wurzelartig an den Klebeflächen geführt wird.
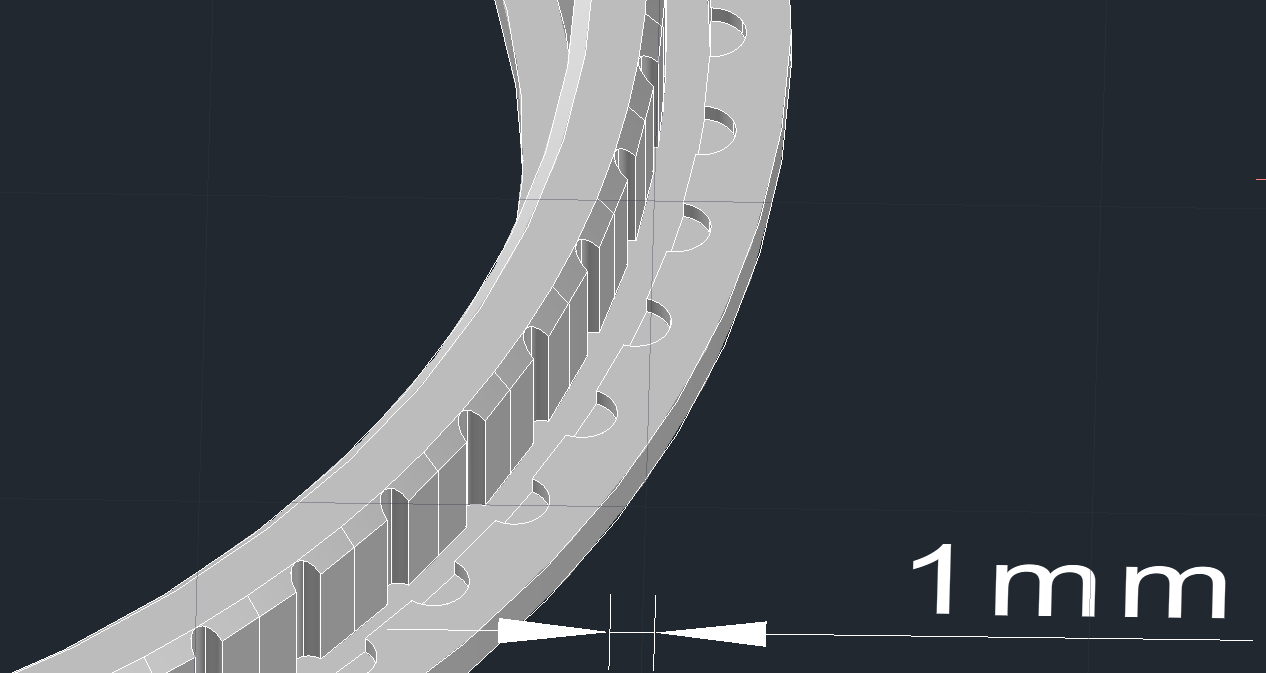
Noch ein letztes Wort zum Thema Einpressmuttern: für den 3D-Druck eignen sich spezielle Einpressmuttern wie von der Firma ruthex besonders:
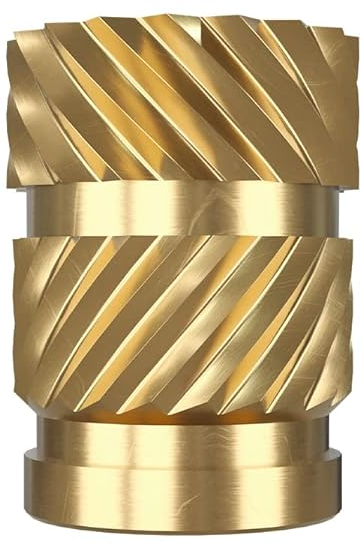
Die Hersteller bieten zu den Einpressmuttern auch passende Einpresswerkzeuge an, welche passend für Lötkolbenköpfe wie z.B. 900M oder T18 erstellt sind. Von einer freihändigen Arbeit beim Einpressen ist abzuraten. Vielmehr sollte ein passendes Einpresswerkzeug mit Führung genutzt werden. Eine andere Möglichkeit besteht in der Verwendung normaler Sechskantmuttern. Im Kunststoff werden dazu passende Vertiefungen minimal kleiner als die Muttern gedruckt. Diese werden nach dem Druck in die Vertiefungen eingepresst.