3D Druck hat mein berufliches Leben mit entscheidend verändert. Ideen sonst nur auf Papier ließen sich auf einmal „materialisieren“ und testen. Allerdings ist 3D Druck kein Allheilmittel und aus meiner Sicht wird zu viel versprochen. Jedes 3D Druckverfahren hat seine Stärken und Schwächen. Auch ist die Konstruktion eines Bauteils stark vom jeweiligen Druckverfahren abhängig.
Aus meiner Sicht gehören zu den wesentlichsten Druckverfahren:
- Fused Deposition Modeling (FDM)
- StereoLithography Apparatus / Digital Light Processing (SLA / DLP)
- Selektives Lasersintern / Selektives Laserschmelzen (SLS / SLM)
- Multi-Jet Modelling (MJF)
Das FDM Verfahren dürfte allgemein bekannt sein. Kunststoff-Filamente werden geschmolzen und schichtenweise übereinander aufgetragen. Es werden also thermoplastische Kunststoffe verwendet. Was damit möglich ist anhand einiger Bilder mit großen und kleinen Teilen und verschiedenen Anwendungen:
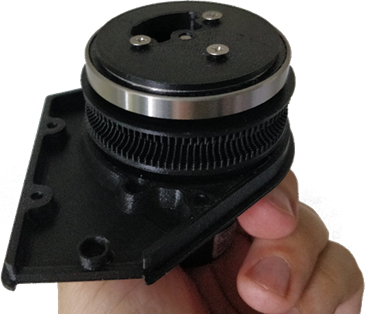
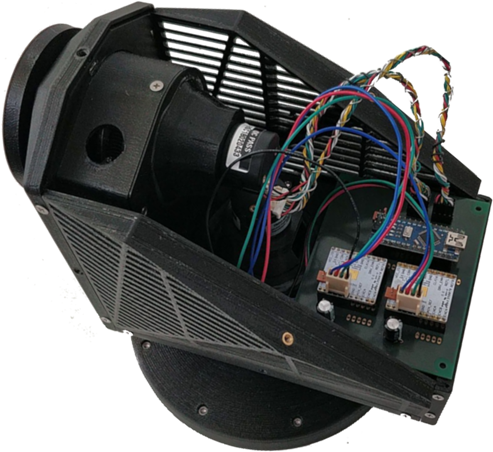
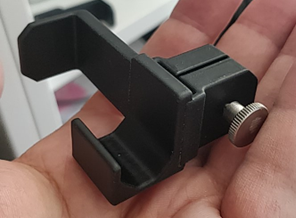
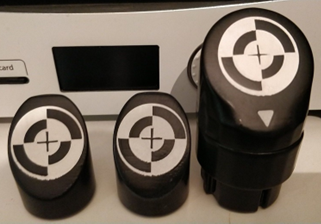
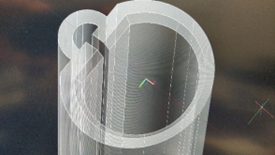
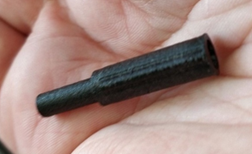
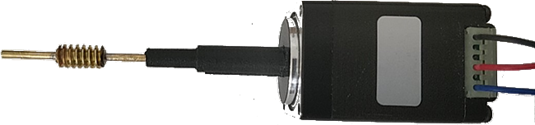
FMD ist ein vergleichsweise sehr einfaches Druckverfahren. Sehr zu empfehlen sind beheiztes Druckbett, geschlossener Bauraum und Dual Extruder z.B. für Supportmaterial. Meine Erfahrung: in den letzten 10 Jahren wurden im Bereich der Filamente starke Fortschritte gemacht. Mit dem richtigen Drucker und guten Einstellungen lassen sich heute viele Kunststoffsorten mit „schwierigem Ruf“ vergleichsweise einfach drucken.
Das schichtweise Arbeitsverfahren von FDM bringt eines seiner Hauptprobleme, die Layerhaftung. Materialeigenschaften aus z.B. dem Spritzguss lassen sich nicht einfach auf FDM übertragen. Als Beispiel seien ABS und ASA genannt. Diese nutze ich vorrangig bei Teilen für Funktionsprototypen, wo hohe Genauigkeiten erreicht und oft geklebt werden muss. Der Preis: die Stabilität ist in der XY-, also Layerebene wesentlich höher als in der Z-Ausrichtung, der Layer übereinander. Der Bruch erfolgt vorrangig zwischen den Layern. Gleiches gilt bei der Alterung. Bei großen Funktionsteilen entstehen im Laufe der Zeit, besonders bei stark wechselnden Temperaturen, Risse zwischen den Layern. Nicht vergessen darf man in der Liste noch ABS-PC, eine Mischung aus ABS und Polycarbonat. Diese bringt noch mehr Steifigkeit und Stabilität in den Druck.
Als in dieser Disziplin positive Gegenbeispiele seien PETG / CPE und Polyamide (PA, als Nylon bekannt) genannt. Diese Gruppen von Kunststoffen verschmelzen sehr gut in den Layern. Ich bevorzuge sie bei Funktionsprototypen daher bei Teilen, wo es besonders auf die Layerhaftung und Beständigkeit ankommt. Dafür sind hier die erreichbaren Genauigkeiten geringer. Polyamide gelten als fast unzerstörbare Filamente. Sie sind biegsam, haben je nach Typ eine gute Hitzeresistenz und sehr gute Gleiteigenschaften. Daher sind sie auch für Gleitlager und Zahnräder ideal. PETG lässt sich mit Dichlormethan noch relativ einfach und stabil untereinander verkleben, bei Polyamiden hilft hochprozentige Ameisensäure (Methansäure).
Nicht vergessen darf man in der Liste noch Spezialkunststoffe, z.B. für Gleitlager. Hier hat sich die Firma IGUS einen Namen gemacht, sie hat sowohl diverse Filamente als auch Pulver (für SLS) und Resin (für SLA) im Angebot.
Bei FDM wird wie beschrieben der Druck beginnend auf einer Druckplatte Layer auf Layer nach oben gedruckt. Der Extruder drückt dabei den erhitzen flüssigen Kunststoff gegen die Druckplatte oder den darunter bereits gedruckten Layer. Durch den Druck nimmt der Kunststoff dabei seine rechteckähnliche Form an und verbindet sich mit dem umliegenden Material. Wird der Kunststoff dagegen „in der Luft hängend“ frei gedruckt, so formt er sich zu einem isoliert hängenden Faden. Bei Überhängen sind daher Stützstrukturen nötig. Bis etwa 45° (von verschiedenen Faktoren abhängig) Neigungen ist ein Druck ohne Stützstrukturen noch sinnvoll möglich.
FDM erlaubt mir, nötige Teile sehr schnell und kostengünstig „in house“ zu fertigen, also in der „fließenden“ Arbeit. Dieser Beitrag geht darauf ein, Teile konstruktiv ideal für FDM zu modellieren.
Ein weiteres Verfahren, mit dem ich gute Erfahrungen gemacht habe, ist Multi Jet Fusion. Es wird hauptsächlich für Polyamide angewendet, hier in Pulverform. Das Pulver wird schichtenweise aufgetragen, danach eine Flüssigkeit, welche die Wärmeabsorption verbessert. Anschließend erfolgt unter Infrarotbestrahlung der Schmelzvorgang der Schicht. Danach wird eine weitere Flüssigkeit aufgetragen, welche den Wärmetransport herabsetzt. Mit ihr wird eine bessere Trennung des 3D Drucks zum restlichen Pulver erreicht. MJF besticht durch mehrere Vorteile. Dazu gehört eine fast 100%ige Materialdichte des 3D Drucks und die gleiche mechanische Festigkeit in alle Richtungen. Ich lasse MJF vom Dienstleister drucken. Die Kosten sind wesentlich höher als in FDM, ein einzelner Griff wie in nachfolgenden Bild gezeigt kostet bereits über 70 Euro. Daher erfolgt der Druckauftrag MJF erst spät im Entwicklungsprozess nach ersten Testdurchläufen in FDM. Bereits bei diesen kann man mit dem richtigen Material Bruchstellen etc. lokalisieren und das CAD-Modell anpassen.
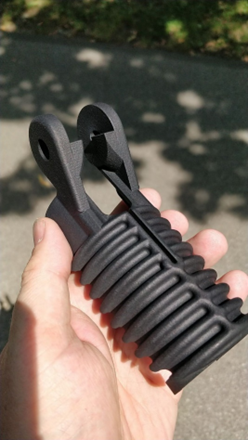
Beitrag wird fortgesetzt …